Bleckmann – Peter Wolterinck Betontechnoloog
Circulaire bouwmaterialen en technieken in de praktijk: het Bleckmann-fulfillmentcenter
Het gebruik van duurzame bouwmaterialen en technieken is een belangrijke factor bij het bouwen van toekomstbestendige panden. Het grootste aantoonbaar circulaire fulfillmentcenter van Nederland, dat van snelgroeiende logistiek dienstverlener Bleckmann op het XL Businesspark in Almelo, is daar een perfect voorbeeld van. Hoofdaannemer VDR Bouwgroep schakelde vloerbedrijf Van Berlo en betonmortelleverancier Rouwmaat in voor het betonwerk.
Bleckmann investeerde bewust in circulaire nieuwbouw. “Traditionele bouw had geld bespaard, maar daar is juist bewust niet voor gekozen”, aldus Bleckmanns directielid Mark van Onna. Voor Bleckmann was circulariteit van de toegepaste bouwmaterialen een harde eis, omdat zij geen (sloop)afval willen achterlaten voor toekomstige generaties. Elk component, van schroeven tot dakplaten en kozijnen, moet aan het einde van de gebruiksduur worden teruggenomen. Dit geldt ook voor het beton dat wordt gebruikt voor fundering, vloeren en laadkuilen. Daarnaast bestaat het beton van het gebouw voor een groot deel uit secundaire grondstoffen. De twee laadkuilen bij de laaddocks zijn bijvoorbeeld gerealiseerd met toepassing van regenwater en betongranulaat, afkomstig van de ontmanteling van een oude woonwijk. En bij een van de laadkuilen is 50% gerecycled grind toegepast.
Impact beton onder de loep
VDR Bouwgroep had eerder in 2018 al een circulaire bouwmethodiek ontwikkeld voor distributiecentra en magazijnen, genaamd Nexteria. Beton is daarbij nog altijd het meest gebruikte bouwmateriaal voor funderingen, laadkuilen, vloeren en wanden. Zo ook voor het circulaire distributiecentrum van Bleckmann, waarin in totaal zo’n 1.000 vrachten voor 52.000 m2 vloeroppervlak beton is verwerkt. Peter Wolterinck, betontechnoloog bij Rouwmaat, stelt “dat beton zeer sterk is en decennialang meegaat, wat het duurzaam maakt in die zin. De impact van beton op het milieu ligt echter al geruime tijd onder een vergrootglas.” Beton bestaat immers uit zand, grind, cement en water. Natuurlijke grondstoffen die langzaam uitgeput raken. Daarnaast kost het produceren van cement - vooralsnog afkomstig van fossiele brandstoffen – veel energie, terwijl cement in sommige projecten vervangen kan worden door milieuvriendelijke alternatieven.
Beton uit oude woonwijken
Met het oog op duurzaamheid, besloot Rouwmaat het eigen productieproces anders aan te pakken. “In plaats van enkel zand en grind uit winningen te gebruiken, maken wij ook zelf grind- en zandvervangers, bijvoorbeeld van beton afkomstig uit oude woonwijken en bedrijfspanden”, vertelt Wolterinck. “Door het beton te breken tot de gewenste korrelgrootte, het zand eruit te zeven en het betongranulaat te wassen, kunnen wij nieuw beton maken met brekerzand, granulaat, cement en regenwater.” Deze bewuste keuze zorgt voor een veel lagere milieubelasting en maakt het mogelijk om beton oneindig vaak te recyclen zonder afval te produceren. Een belangrijke ontwikkeling die bijdraagt aan de opvallend lage MPG (Milieu Prestatie Gebouw) en de hoge mate van circulariteit (MCI, Materialen Circulariteit Index) in het gebouw van Bleckmann.
Omdat er een berekende toekomstige puntbelasting was en de grond onder het pand niet stabiel genoeg was, moest het gebouw worden versterkt door middel van onderheien. De toegepaste mini-vibropalen werden door Van Berlo grondig herzien om ze duurzamer en minder milieubelastend te maken. Voor de fundatie van het distributiecentrum leverde Rouwmaat beton dat gemaakt was van gerecycled betongranulaat en regenwater. Het niet-constructieve deel van de fundering werd volledig vervangen door circulair betongranulaat, wat nieuw was. Voor de constructieve delen van de fundering werd de "standaard" maximaal toegestane 30% betongranulaat gebruikt.
Uitdagingen met de vloer
Kevin Hulskamp, hoofd projectmanagement bij Van Berlo, vertelt: "We hebben in onze mini-vibropalen 30% van het normale grind vervangen door gerecycled puingranulaat. We maakten twee typen laadkuilvloeren. Die zijn beide met een ander, duurzamer materiaal geproduceerd dan het standaard grind.” In samenspraak met Rouwmaat werd er gekozen voor een laadkuilvloer waarbij 50% van het benodigde primaire riviergrind vervangen werd door betongranulaat (Betongranulaat 8/16 TRM). Bij de tweede laadkuil is 50% van het benodigde primaire riviergrind vervangen door thermisch gereinigd teerhoudend asfalt (Eco-granulaat 8/16). “Wij kiezen ook heel sterk voor kwaliteit”, benadrukt Hulskamp. “We ontwikkelen ook onze eigen mengsels en hebben onze eigen research- & development-afdeling die onderzoekt hoe we ons beton en de vloeren zo optimaal mogelijk duurzaam en circulair kunnen maken. Het is een thema in de markt waar je niet meer omheen kan.”
Bij het ontwerp van het fulfillmentcenter moest er rekening worden gehouden met verschillende eisen, zoals het draagvermogen van de vloer en de vlakheid ervan. “Hoewel er een voorkeur was voor het gebruik van circulaire grondstoffen, was het niet altijd mogelijk om hieraan te voldoen”, vertelt Hulskamp. “Vooral omdat het een smal gangensysteem betreft met hoge vlakheidseisen en een zware vloerbelasting. Ondanks deze grote uitdagingen is het ons gelukt om aan de gestelde eisen te voldoen.”
De grootste uitdaging binnen dit project lag volgens Van Berlo bij de druklagen, oftewel de mezzaninevloeren in het warehouse. Hulskamp legt uit: “Normaal gesproken worden daar kanaalplaatvloeren gebruikt en wordt er daarbovenop een constructieve druklaag gestort. Voor dit project was er een speciale tussenlaag nodig om ervoor te zorgen dat de vloeren los van elkaar zouden blijven liggen. Dit was nodig om de vloer losmaakbaar te houden en de staalconstructie en de kanaalplaatvloeren te zijner tijd weer op een andere plek te kunnen toepassen.”
Hoop voor een groene toekomst
Dit project voor Bleckmann is een inspirerend voorbeeld van hoe duurzame en circulaire bouwmaterialen en technieken kunnen worden toegepast om toekomstbestendige panden te bouwen. Door de intensieve samenwerking tussen VDR Bouwgroep, Van Berlo en Rouwmaat konden voor de beton-gerelateerde vraagstukken betrouwbare en hoogwaardige oplossingen worden gevonden. Dit project bewijst dat met een doordachte aanpak en de juiste partners, zelfs de grootste bouwprojecten kunnen bijdragen aan een groene toekomst.
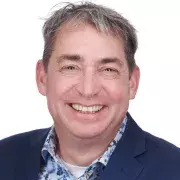