Bouw van een demonstratiefabriek voor het scheiden van CO2 tijdens cementproductie in Lixhe (B) (foto: Paul Poels)
Cementindustrie is op verschillende vlakken bezig met terugbrengen van de CO₂-uitstoot
Er zijn veel mogelijkheden om het gebruik van beton duurzamer te maken. Denk aan cementvervangers als vliegas, hoogovenslakken, een het 1-op-1 hergebruik van betonnen elementen, het inzetten van alternatieve bindmiddelen of het milieuvriendelijker maken van de cementproductie. Op deze laatste mogelijkheid gaan we in dit artikel dieper in. Bij de productie van traditioneel Portlandcement komt CO₂ vrij. Dat gebeurt bij het verhitten van de gemalen kalksteen. De daarin opgeslagen CO₂ komt daarbij in de atmostfeer. Het afvangen van het koolzuurgas is lastig omdat er ook andere gassen vrijkomen.
De cementindustrie is echter bezig met methoden om bij de productie CO₂ uit de gassen te halen, waarna het opgeslagen of gebruikt kan worden. Dat proces noemen we Carbon Capture en Storage (CSS) Dat staat voor koolstofafvang en -opslag. Op die manier komt het broeikasgas niet in de atmosfeer en kan het dus ook niet bijdragen aan de opwarming van de aarde. Om het succesvol te maken is het van belang om tegen aanvaardbare kosten en energieverbruik CO₂ uit de gassen te halen die vrijkomen in het productieproces. Verder moet het proces efficiënt zijn en moet de CO₂ die eruit wordt gehaald heel zuiver zijn.
CO₂ oplossingen cementindustrie
Daar zijn drie soorten oplossingen voor bedacht. We beginnen met de Post-combustion (naverbranding). Bij dat afvangproces scheiden producenten de rookgassen voordat ze de schoorsteen verlaten. Dat kun je op verschillende manieren doen, maar het werken met zogeheten regeneratieve reactoren op basis van amines (organische stoffen die zijn afgeleid van ammoniak) vormen op dit moment de meest geavanceerde technologie. Deze methode wordt al bijna dertig jaar in de olie-industrie toegepast. In de cementindustrie loopt er een succesvolle pilot in de Norcemfabriek in het Noorse Brevik. Dat is een project dat eind 2024 op industriële schaal zal draaien. Daar zal dan tot 400.000 ton CO₂ worden afgevangen.
Zuivere zuurstof
Oxyfuel-verbranding is een andere methode om te voorkomen dat veel CO₂ de schoorsteen verlaat. Daarbij wordt er bij de verhitting van de klinker in plaats van lucht zuivere zuurstof toegevoegd. Zo komt er naast CO₂ alleen maar waterdamp vrij, wat het relatief eenvoudig maakt om het koolzuurgas eruit te filteren en op te vangen. Daarnaast is er nog de technologie waarbij de CO₂ al direct gescheiden wordt. Bij het tot nu toe normale proces gaat vermalen kalksteen een voorverwarmoven. Daarbij komt de CO₂ uit het gesteente vrij. Daarna gaat het naar de draaioven waarin zich op een temperatuur van 1450 graden Celsius klinker vormt, het belangrijkste bestanddeel van cement. Het vrijkomende CO₂ vermengt zich met de rookgassen van de verbranding en is er niet meer uit te filteren.
Scheiden in een aparte buis
In het Belgische Lixhe werkt Heidelberg Materials aan de LEILAC-1. Daar is een techniek toegepast die het wèl mogelijk maakt het koolzuurgas afkomstig van de kalksteen te scheiden van de rest. Daar valt de vermalen kalksteen in een afgesloten stalen buis voordat het de oven in loopt. De stalen buis wordt van buitenaf verhit waardoor de kalksteen binnenin de buis wordt gesplitst in calciumoxide (CaO) en zuivere CO₂ die kan worden afgevangen. Zo blijven de ovengassen en de CO2 die vrijkomt bij de ontleding van kalksteen van elkaar gescheiden. LEILAC staat voor Low Emissions Intensity Lime And Cement, oftewel kalk en cement met een lage emissie-intensiteit. De resultaten in Lixhe zijn hoopvol. In Hannover, Duitsland zijn de voorbereidingen gaande voor de opening van een tweede LEILAC-fabriek met een capaciteit die vier keer zo groot is.
Geschiedenis LEILAC-1
Het verhaal van de LEILAC-1 begint in 2014 als het Australische technologiebedrijf Calix een reactor bouwt die CO₂ van magnesiummaterialen kan scheiden. Een jaar later vormt het bedrijf een consortium om de werkende technologie toe te passen op cement en kalk. Dat leidt in 2016 tot de het pilotproject LEILAC-1. In 2019 opent die demonstratiefabriek. De productiecapaciteit is dan 25.000 ton CO₂-vrije portlandcementklinker per jaar. Omdat het om tests gaat, verdwijnt de apart opgevangen CO₂ voorlopig in de atmosfeer, zoals normaal. Als de tests slagen en het proces ook op grotere schaal kan worden toegepast, dan is de milieuwinst enorm. Dan is het namelijk mogelijk om cement te maken zonder dat er koolzuurgas in de lucht komt. Dan kan het CO₂ in lege gasvelden worden gepompt of als grondstof dienen. Bij het proces in de LEILAC-1 was de stalen buis waarin de kalksteen wordt verhit het kritische punt in het proces. De temperaturen worden daarbij namelijk zo hoog dat staal normaal gesproken smelt. Inmiddels gebruikt men in Lixhe een innovatieve stalen buis die de warmte kan doorgeven zonder te smelten.
Schaalbare oplossing
Het Internationaal Energieagentschap (IEA) beschouwt het afvangen van CO₂ als de enige schaalbare oplossing in de cementindustrie. Er zijn wel alternatieven die cement kunnen vervangen, maar daarbij gaat het om nichemarkten zegt Jan Theulen, die bij het Duitse moederbedrijf van Heidelberg Materials de leiding heeft over alles van CO₂-afvang en -hergebruik: ,,Beton speelt zo’n alomtegenwoordige rol in de moderne maatschappij dat alleen de grootschalige oplossingen ons echt vooruit zullen helpen. Na water is cement de meest gebruikte grondstof”, zegt hij in het Belgische magazine De Tijd. Met het afvangen van broeikasgas tijdens de productie van klinker is weliswaar een belangrijke stap gezet naar het klimaatneutraal produceren van cement. Zo moet nog een alternatief worden gevonden voor het verwarmen van de ovens met aardgas. De ovens zouden elektrisch verwarmd kunnen worden, maar dan is de vraag of er voldoende hernieuwbare energie voorhanden is.
LEILAC-2
Na de ‘zeer goede resultaten’ in België besloot Heidelberg Materials samen met Calix en een Europees consortium een tweede demonstratie-installatie te bouwen: de LEILAC-2. Die proeffabriek komt in Hannover en kan vier keer zoveel cement produceren zonder CO₂-uitstoot als LEILAC-1. Die vangt jaarlijks 25.000 ton broeikasgas af, LEILAC-2 heeft een capaciteit van 100.000 ton. Met deze opschaling zet het bedrijf een flinke stap. Als de installatie in gebruik is genomen en de productie op stoom is, kan Heidelberg Materials twintig procent van al het in Hannover geproduceerde cement maken zonder CO₂-uitstoot.
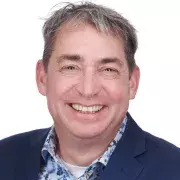