De Italiaanse architectuurstudio Mario Cucinella Architects en 3D-printen WASP hebben een prototype geprinte woning gemaakt van lokale ruwe aarde en gecalcineerde klei. Deze woning combineert de 3D-technologie en het gebruik van lokaal gewonnen materiaal.
Kan 3D-betonprinten een revolutie teweegbrengen in duurzaam bouwen?
Het zal de bouwwereld niet zijn ontgaan: 3D-printen van beton. De ontwikkelingen met deze innovatieve techniek gaan razendsnel. Mede dankzij de opkomst van de 3D-printers is er nog veel meer mogelijk. Er zijn al verschillende gebouwen en constructies met beton geprint. Kan 3D-betonprinten een revolutie teweegbrengen in duurzaam bouwen? In dit artikel een aantal voorbeelden.
Technologische innovaties hebben geleid tot onconventionele technieken en materialen. Dat zorgt vaak niet alleen voor een lagere milieubelasting, maar verhoogt ook de levensduur en sterkte van het gebouw. Denk aan het gebruik van materialen zoals bamboe, recyclebaar afval, recyclebaar plastic, bitumenmaterialen, gehard glas en kruimelrubber. Op deze lange lijst staan ook materialen zoals vezelversterkt polymeer, glasvezelversterkte kunststoffen en met bamboe versterkte kunststoffen. Het zijn stuk voor stuk bijzondere ontwikkelingen, maar huizen uit de 3D-betonprinter zijn zonder twijfel de meest verbluffende innovatie van deze tijd. Een 3D-printer stapelt beton of een ander bouwmateriaal in laagjes op elkaar. Bij deze techniek wordt een pastamateriaal door een buisje uitgestoten. Dit kan beton zijn, maar ook aardachtige materialen. Door het stapelen in lagen ontstaat een ruimtelijk volume.
Technologische innovaties woningbouw
Deze 3D-print technologie bespaart in vergelijking met traditionele bouwmethoden tijd, moeite en materiaal. Het 3D-betonprinten beperkt zich vooralsnog tot het maken van muren en frames, maar de technologische ontwikkelingen gaan snel. In een later stadium van het bouwproces worden ramen en sanitair conventioneel geïnstalleerd. De eerste 3D bekistingsconstructies zijn al een feit. Ondanks deze beperkingen wint de technologie aan kracht. Dat is te danken aan de grote technologische snelheid van 3D-printen. Inmiddels is printen de laboratoriumfase allang voorbij en staat er in Eindhoven al een 3D-printfabriek. Tijd om eens wat bouwwerken en constructies achter elkaar te zetten en te kijken of deze ook duurzaam zijn.
Project Milestone
Milestone is de eerste 3D-geprinte huurwoning. Deze keivormige woning in Eindhoven is ontworpen door Studio Houben & Van Mierlo. Het is ontwikkeld als onderdeel van een onderzoeksproject met de Technische Universiteit Eindhoven. Het hele bouwproces kun je het beste omschrijven als een nieuwe leerervaring. Met het maken van deze woning is de kennis rondom de productie van 3D-geprinte woningen verbreed. De eerste van de vijf woningen in het project Milestone in Eindhoven werden nog in het laboratorium in delen geprint en dan ter plaatse gemonteerd. Het ontwerp is daarop aangepast: de ramen en deuren zijn precies tussen de verschillende delen in geplaatst. Nu nog onder geconditioneerde omstandigheden, maar het doel is om uiteindelijk de woningen op locatie te kunnen printen. Duurzaam gemaakt en energiezuinig, maar ook een behaaglijk, licht en stil huis. In een fantastische natuurlijke bosrijke omgeving. De eerste woningen zijn opgeleverd. Lees het verhaal van de bewoners.
East 17th Street Residences
Een ander voorbeeld van 3D-geprinte woningen vinden we in de Verenigde Staten. Daar staat East 17th Street Residences. Deze zijn ontworpen om extreme weersomstandigheden te weerstaan. De constructie werd in zeven dagen voltooid. Het bouwwerk heeft woningen met twee, drie en vier slaapkamers. Tot nu toe hebben deze op cement gebaseerde huizen een aardbeving met een kracht van 7,4 op de schaal van Richter en zware winterstormen doorstaan. Dit laat zien hoe de 3D-printconstructie betrouwbaar is en bestand tegen natuurgeweld.
Costa Den helder
Een prachtig voorbeeld van de prefab 3D-betonprintmethode is Costa in Den Helder. Kokon Architectuur & Stedenbouw heeft met de techniek een ware metamorfose gecreëerd. Van monotone galerijflats naar een fraaie mediterrane verschijning, inclusief ruime balkons voor de bewoners. Twee gedateerde jaren ’70-flats aan de Hendrik Baskeweg zijn getransformeerd tot prachtige sculpturale appartementengebouwen. Met dank aan bijna 1.200 prefab betonelementen, variërend van 2 tot 12 vierkante meter. Lees meer over dit project.
Tecla
In samenwerking met 3D-printspecialisten WASP heeft de in Italië gevestigde studio Mario Cucinella Architects dit prototype van een koolstofarme behuizing ontwikkeld. Het draagt de naam Tecla en bestaat uit een ruimtelijk omhulsel van twee met elkaar verbonden koepels met een totale oppervlakte van ongeveer 60 vierkante meter. Het grote dakraam aan de bovenkant van elke koepel laat licht van bovenaf de ruimte binnendringen, waardoor de koepels natuurlijk goed verlicht worden. De combinatie van moderne technologie, lokaal geproduceerde klei als bouwmateriaal en de 3D-printer laat zien hoe functionaliteit en esthetiek elkaar kruisen.
Two-Story Detached House
Het Two-Story Detached House is het allereerste 3D-geprinte huis in Duitsland. Het heeft een twee verdiepingen tellende structuur met ongeveer 860 vierkante meter bewoonbare ruimte per verdieping. Het huis is gebouwd met behulp van een 3D-printer met de naam BOD2, ontwikkeld door de Deense fabrikant COBOD. Het belangrijkste kenmerk van deze machine is dat het al tijdens het printen de toevoeging van leidingen en andere interne bouwservicecomponenten mogelijk maakt. Bovendien kan hij tot tien vierkante meter dubbelwandige wand printen in slechts vijf minuten. Bekijk hier de foto's van het huis.
Kamp C
Op Kamp C, het provinciaal Centrum voor Duurzaamheid en Innovatie in de bouw, in Westerlo, België, werd een huis geprint met de grootste 3D-betonprinter van Europa. De woning is negentig vierkante meter groot en werd in één stuk geprint met een vaststaande printer. Dat is een wereldprimeur. Het huis is ontworpen als energiezuinige woning en heeft voorzieningen zoals plafond- en vloerverwarming, zonnepanelen en een warmtepomp. Het geprinte huis is drie keer sterker omdat de druksterkte van het materiaal drie keer hoger is dan de klassieke baksteen.
3D-Betonprinten in de GWW
Fietsbruggen in Noord-Brabant en Noord-Holland zijn het eerste bewijs: 3D geprint beton vindt zijn weg ook in de Grond Weg -en Waterbouw. In de agrarische sector zijn nog geen initiatieven met 3D-geprint beton. Toch kan het voor specifieke conceptstallen, naadloze opslagkelders, esthetische bijgebouwen of alleen gebouwonderdelen, zoals gevels, een meer dan goede optie zijn. Het grote voordeel van 3D-beton is het vormvrij kunnen bouwen en 3D-printen draagt bij aan het ontwikkelen van constructies met een hoge esthetische waarde.
Striatius
In een tuin in Venetië staat een prachtige nieuwe betonnen brug. Het is een bijzonder en innovatief bouwwerk. De brug komt namelijk uit de 3D-printer, heeft geen wapening en is volledig te demonteren. Bovendien is er veel minder beton gebruikt dan wanneer er op traditionele wijze gebouwd zou zijn. Het is een blauwdruk voor duurzaam bouwen met beton. De brug is gebouwd door Block Research Group van de Zwitserse universiteit ETH Zürich en de Computation and Design Group van Zaha Hadid Architects (ZHA CODE), in samenwerking met beton-3D-printspecialisten incremental3D. Het bedrijf Holcim leverde het mengsel voor deze brug. Lees meer over deze brug.
Eggshell Pavilion
Dit demonstratieproject is een systeem van vier kolommen en vier geribbelde platen die naar behoefte kunnen worden gedemonteerd, vervoerd en weer in elkaar gezet. Het ontwerp van het paviljoen is gebaseerd op algoritmen die de geometrie van de architectuur genereren in overeenstemming met de fabricagegegevens voor het 3D-printproces. Het ontwerp wordt vervolgens vertaald naar een flinterdunne 3D-geprinte bekisting van glasvezelversterkt PET-G die gedeeltelijk is gerecycled van eerdere vormen (drie millimeter voor de kolommen en vijf voor de plaat).
Traditionele stalen wapening wordt vervolgens in de bekisting geplaatst voordat het beton wordt gestort. De kolommen zijn gemaakt met een digitaal gestuurd systeem dat gebruikmaakt van snel uithardend beton. Zodra het beton is uitgehard, wordt de vorm afgesneden, vermalen tot pellets en teruggeplaatst in de trechter van de 3D-printer om de volgende set bekistingsmallen te maken. Een techniek die geschikt is voor kolommen. Het printen met bio-plastic wordt ook toegepast door DUS Architects. Die met behulp van duurzame bio-plastics en beton een klein huis in Amsterdam heeft ontworpen.
Fietsbrug Gemert
Gemert (Noord Brabant) beleefde eind 2017 een wereldprimeur: de eerste volledig constructieve, geprinte brug werd geopend. Vanwege ontbrekende ontwerpregels speelde 'design by testing' bij de realisatie een grote rol. De brug is 8 meter lang en bestaat uit 800 laagjes betonmortel. Hiervoor is geen mal gebouwd waar het beton in wordt gestort. En er zijn minder mensen buiten nodig voor het uitzetten van de maatvoering. Voorbereidingen zijn hierdoor veel minder. De brug is geplaatst tussen de N605 (Volkel-Gemert) en de N272 (Beek en Donk-Boxmeer).
Fietsbrug Nijmegen
De langste 3D-geprinte betonnen brug ter wereld staat in Nijmegen. Specialisten van BAM Infra en Weber Beamix hebben bijna honderd onderdelen van de brug in een fabriek geprint. De onderdelen passen als een legpuzzel in elkaar. Er zitten zelfs uitsparingen in om het beton te kunnen spannen. De brug is ontworpen door architect Michiel van der Kley, in opdracht van Rijkswaterstaat en wordt gerealiseerd in samenwerking met de Technische Universiteit Eindhoven als kennispartner. Weber Beamix, BAM Infra, Summum Engineering en Witteveen+Bos zijn betrokken marktpartijen. In 2020 sprak Betonhuis met Jean de Nijs, projectmanager N243 van de provincie Noord-Holland. Ook in die provincie wordt 3D-geprint beton voor vier nieuwe bruggen toegepast.
Duurzaam
Het toepassen van 3D-printtechnologie biedt kansen voor het ontwerp en de realisatie van constructieve toepassingen in de bouw. Het biedt vrijheid in het ontwerp en de 3D-ontwerpomgeving rekent aanpassingen direct door. Het ontwerp is vertaald in een code waarmee de printer het ontwerp produceert. Door dit digitale ontwerp- en uitvoeringsproces dalen de faalkosten en heb je tekeningen niet meer nodig. Door optimaal te ontwerpen is minder materiaal nodig vergeleken met traditioneel geproduceerde bruggen met bekistingen. De printer legt namelijk alleen beton neer daar waar het nodig is voor de constructieve sterkte van de brug. Een besparing van 30% is haalbaar. 3D-betonprinten werkt zonder bekistingen en dat scheelt arbeid en maakt het mogelijk zonder restafval te bouwen.
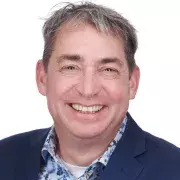